In our previous newsletters, we’ve touched on the field deployments in Gulkana and Greenland for the Seismometer to Investigate Ice and Ocean Structure (SIIOS). These functioned as a dress rehearsal for future missions to Europa, the icy moon of Jupiter. On the other side of this research is the development of the actual instrument that will be sent for deployment. In this post, we will delve into the journey of sensor development, from testing mechanics and robustness, to overcoming obstacles and the quest for planetary protection.
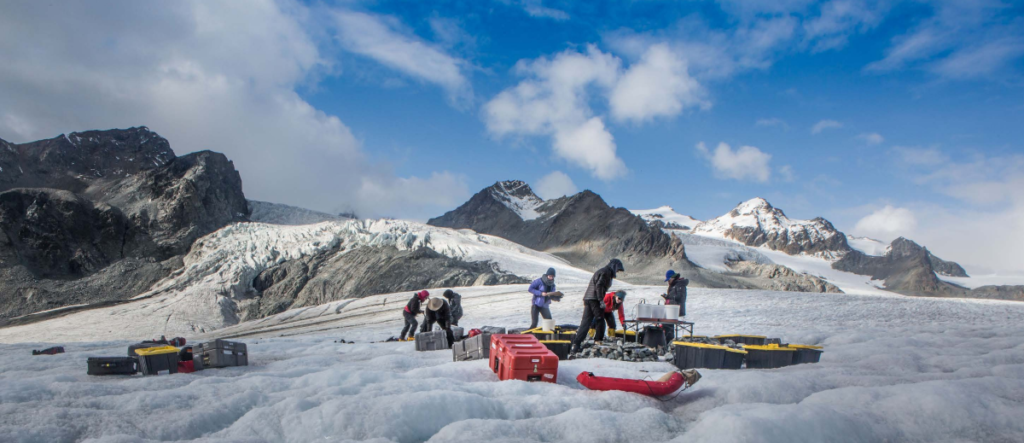
As the design of the instrument progressed there were a battery of tests to mature the design through the NASA Technology Readiness Levels (TRL). Vibrational and shock tests were conducted to check the robustness of the sensor against conditions encountered during the mission including launch and landing. The vibrational test simulated the vibrations from a launch vehicle, i.e. a big rocket, and was performed on each axis of the sensor for 1 minute. The shock test ensures the sensor can survive an unexpected rough landing.
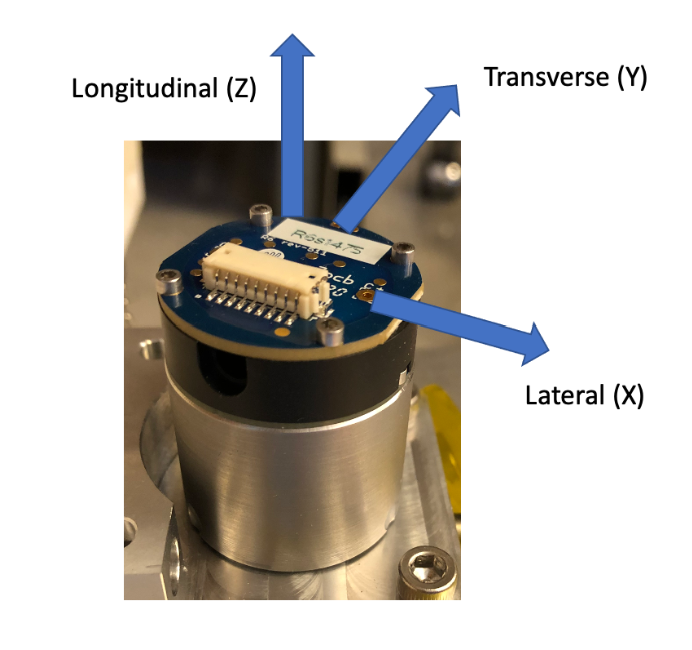
Before sending the sensor off to a third-party lab for a TRL-6 qualification, some tests were done in-house for troubleshooting. In the video below, the sensor is placed on a shaker with parameters modeled from the General Environmental Verification Standards (GEVS) from NASA (GSFC-STD-7000A). During initial tests, springs supporting the proof mass in the sensor were fractured due to metal fatigue. The cyclic loading applied to the spring arms due to the lateral motion of the proof mass induced stress higher than the fatigue strength of the spring material. To prevent this, metal stops were installed around the proof mass and precisely adjusted to limit the lateral motion of the proof mass, which successfully fixed this issue. As an interesting side note, we found there is a noticeable change in the sound of the vibration test when there is a failure that we were able to use as a diagnostic method.
Two thermal tests were also conducted as a part of the TRL-6 qualification. A Thermal-vacuum test (TVAC) was performed to test the sensors survivability under the environmental conditions in space. The sensor was subjected to thermal cycling with temperatures ranging from -55°C to 75°C for about a week and a half in vacuum (10-5 Torr or 0.00000001316 atmospheric pressure). Dry heat microbial reduction (DHMR) was carried out to ensure the sensors survive the rigorous planetary protection protocols put in place to make sure missions don’t send Earth’s microbes to other bodies. In other words, instruments sent out into the solar system are subjected to long exposure to a high temperature in order to rid the devices from any unwanted microbes. Think of it as the barbequing of microbial reduction. The sensor was baked at 130°C for 43 hours. The sensor that was sent for this testing is still running and used in our lab to this day.
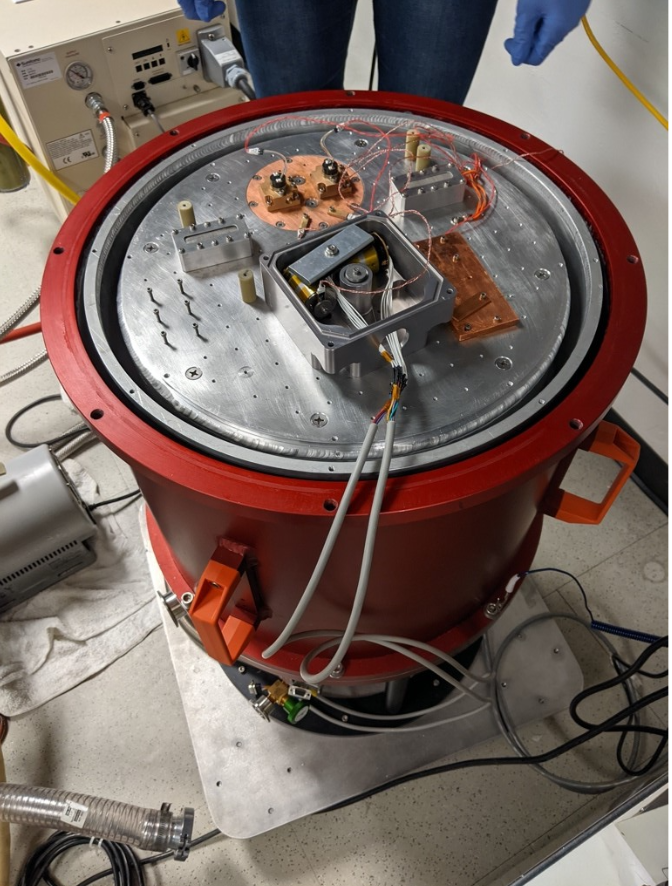
Silicon Audio is getting ready to go through this whole process again with a new larger, higher performance instrument developed for deployment onto an asteroid. Stick around for future updates on this ongoing project once we hit significant milestones!